Discover What is Porosity in Welding and Its Impact on Structural Honesty
Discover What is Porosity in Welding and Its Impact on Structural Honesty
Blog Article
The Science Behind Porosity: A Comprehensive Guide for Welders and Fabricators
Understanding the complex mechanisms behind porosity in welding is vital for welders and producers making every effort for impeccable workmanship. From the composition of the base products to the details of the welding process itself, a wide variety of variables conspire to either worsen or ease the visibility of porosity.
Understanding Porosity in Welding
FIRST SENTENCE:
Assessment of porosity in welding discloses vital understandings into the stability and quality of the weld joint. Porosity, identified by the presence of cavities or gaps within the weld steel, is a typical issue in welding processes. These gaps, if not correctly resolved, can jeopardize the structural stability and mechanical properties of the weld, causing possible failings in the ended up item.
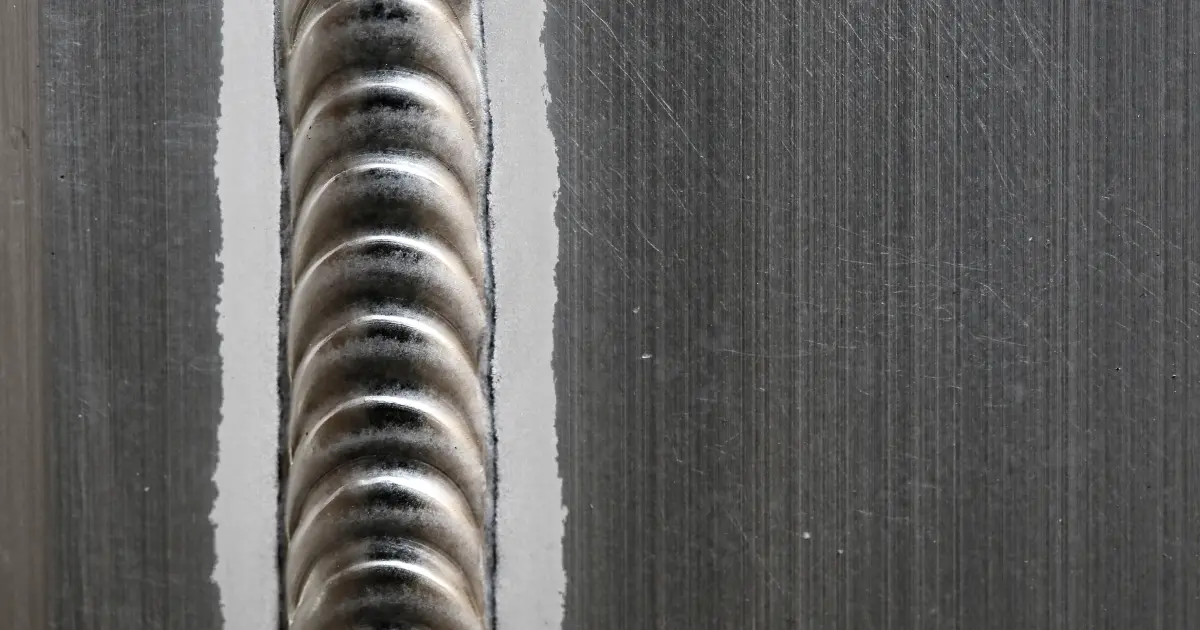
To spot and measure porosity, non-destructive testing approaches such as ultrasonic testing or X-ray assessment are often utilized. These techniques permit the recognition of internal problems without jeopardizing the stability of the weld. By assessing the size, form, and distribution of porosity within a weld, welders can make informed decisions to boost their welding processes and accomplish sounder weld joints.

Elements Influencing Porosity Formation
The occurrence of porosity in welding is influenced by a myriad of elements, ranging from gas securing efficiency to the intricacies of welding parameter setups. Welding parameters, consisting of voltage, existing, travel speed, and electrode type, additionally influence porosity formation. The welding strategy used, such as gas metal arc welding (GMAW) or shielded steel arc welding (SMAW), can affect porosity formation due to variants in heat distribution and gas coverage - click resources What is Porosity.
Effects of Porosity on Weld Quality
The visibility of porosity likewise deteriorates the weld's resistance to deterioration, as the entraped air or gases within the voids can respond with the surrounding atmosphere, leading to deterioration over time. Furthermore, porosity can impede the weld's capacity to hold up against pressure or impact, more endangering the overall top quality and integrity of the welded structure. In crucial applications such as aerospace, auto, or structural buildings, where safety and security and durability are paramount, the destructive results of porosity on weld high quality can have severe consequences, highlighting the importance of decreasing porosity via appropriate welding methods and procedures.
Strategies to Reduce Porosity
In addition, utilizing the ideal welding criteria, such as the right voltage, existing, and take a trip rate, is important in protecting against porosity. Maintaining a constant arc size and angle during welding also aids lower the probability of porosity.

Additionally, choosing the best securing gas and preserving proper gas flow rates are essential in decreasing porosity. Making use of the ideal welding technique, such as back-stepping or using a weaving motion, can also assist disperse warm evenly and reduce the opportunities of porosity development. Last but not least, making sure appropriate ventilation in the welding atmosphere to get rid of any type of possible sources of contamination is important for accomplishing porosity-free welds. By executing these techniques, welders can effectively reduce porosity and create high-quality bonded joints.

Advanced Solutions for Porosity Control
Carrying out cutting-edge technologies and innovative techniques plays a pivotal function in attaining remarkable control over porosity in welding processes. In addition, visit site employing advanced welding strategies such as pulsed MIG welding or customized environment welding can also aid reduce porosity concerns.
Another advanced solution entails using sophisticated welding try this tools. For instance, making use of tools with built-in functions like waveform control and innovative power sources can boost weld top quality and reduce porosity risks. Furthermore, the application of automated welding systems with exact control over specifications can dramatically reduce porosity defects.
Furthermore, incorporating innovative monitoring and evaluation modern technologies such as real-time X-ray imaging or automated ultrasonic testing can assist in discovering porosity early in the welding procedure, permitting prompt corrective activities. In general, incorporating these advanced remedies can considerably enhance porosity control and enhance the overall top quality of welded elements.
Verdict
In final thought, understanding the science behind porosity in welding is essential for welders and producers to produce premium welds - What is Porosity. Advanced solutions for porosity control can even more boost the welding procedure and make sure a solid and reputable weld.
Report this page